In supply chain management software, which usually has to be implemented, individualized and optimized in long, laborious projects together with customers, the app store approach is still new. However, it is SAP’s desired goal – and therefore also GIB’s. As an expert for supply chain optimization in the SAP environment, GIB is currently taking its first steps into the cloud, exploring unknow terrain as it is guided by a new vision of the future.
GIB’s new technologies, which are primarily focused on SAP, are united by a core concept. Customers should also be able to enhance applications that have already been installed with additional functionalities – without the need for time-consuming, cumbersome and costly implementation.
“SAP is our most important partner. As one of its development and service partners, we are always observing closely in which direction SAP is going. We always try to incorporate new technologies and roadmaps in our GIB products as soon as possible to be able to support SAP’s strategy in the long term,” says Nikolaj Schmitz, responsible for SAP technologies and partnership at GIB.
Supply chain management in the cloud
However, implementing this strategy has to take center stage in order to be successful. “To bring our solutions into the cloud, we need to put everything to the test. Which functions can we transfer? Which functions are even suitable for cloud deployments? Furthermore, there are also many unanswered questions concerning fundamental technological basics. For example, which programming language should we work with? The Abap cloud version or Java? Which advantages or challenges will either of them bring? We are currently taking a closer look at all of these topics,” adds Schmitz.
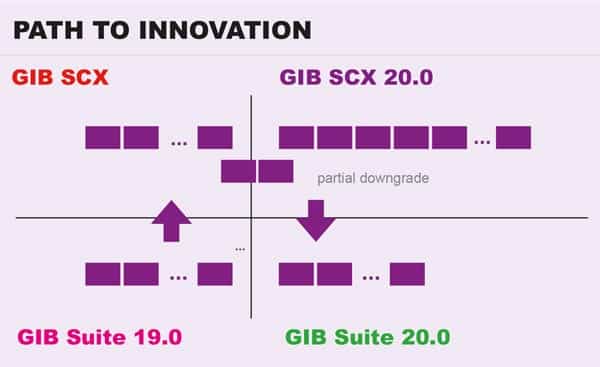
At the same time, GIB is already working on its pilot project for the cloud: the Mobile Maintenance Guide app. It will be the first GIB application available in the cloud through a hybrid approach – the best of both worlds. The Mobile Maintenance Guide App is part of the GIB Shopfloor Integration environment, an IoT solution for connecting machine sensors and ERP systems.
The mobile application, which is already available as on-prem version, displays important data and key figures that are necessary and helpful for maintenance tasks, such as the history of machines including past downtimes and repair times as well as forecasts and predictions. It furthermore provides an overview of important contacts as well as the current stock of spare parts including order deadlines.
The mobile app can also help maintenance technicians navigate large machinery plants by connecting to a navigation application, facilitating part of supply chain management.
“Customers using our Mobile Maintenance Guide often have to navigate large workshops. Rather than using it on a stationary computer, then, most people use it on their mobile phone or tablet. Therefore, the application is particularly well-suited as a hybrid solution with connection to the cloud. The app is anchored in the cloud, but also allows access to required ERP data – following strict security guidelines, of course,” explains Schmitz.
GIB’s cloud story continues
Of course, GIB’s cloud story doesn’t end with just one single application. Besides the Mobile Maintenance Guide app, GIB is also working on other cloud applications. One of them is the KPI Tower, a program for clearly displaying key performance indicators (KPIs) in the modern Fiori design.
In the future, it will ensure staff and especially management always have a quick overview of the most important KPIs at any given place and time. It will also allow them to take the necessary steps to avoid imminent shortcomings, should the situation in question require it.
However, this is not yet where GIB draws the line. In the future, the new suite GIB SCX – Supply Chain Excellence will be available as cloud version on S/4 Hana. Customers will then be able to choose exactly which functionalities they actually need, and use them immediately in the cloud.
This will eliminate necessary implementation efforts, which is especially useful for small and mid-sized businesses because they only have to spare a small amount of resources while supply chain management costs are significantly reduced.
Release changes will be carried out just as quickly and without problems or additional effort. GIB’s vision therefore describes nothing less than an SAP ERP system that offers exactly the functionality that users need, is up to date at all times thanks to cloud connections and can be quickly and easily adapted to new requirements if necessary. It’s a distant dream, but GIB already has the right tools. “There’s still a lot to do before we make that vision a reality, but we are working on it,” says Nikolaj Schmitz.
This is the third article of a series. If you want to read the first one, click here. If you want to read the next one, click here.
Add Comment